The procurement team in the construction industry is responsible for sourcing high-quality products and services with a specific budget and regulatory guidelines in order to successfully operate a business or complete a project. It is believed that a good procurement in construction, which relies on industry knowledge, experience, and the right technology, is synonymous with a successful project.
This article discusses the three best procurement practices that can be implemented by construction companies to achieve the company objectives. These practices involve performing procurement benchmarking, investing in cloud-based procurement tools, and practicing strategic collaboration in procurement.
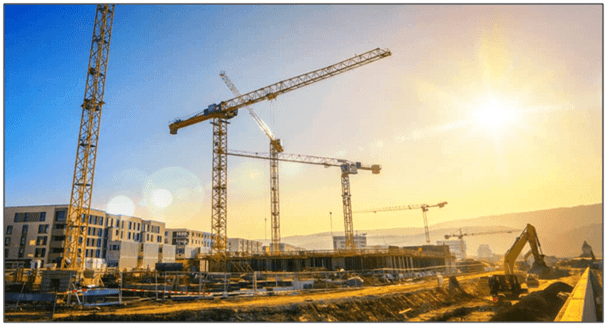
Table of Contents
Performing Procurement Benchmarking
Procurement benchmarking is about measuring the procurement performance and making the appropriate adjustments to help a company to identify new sources of value, pinpoint new capabilities, and make case for change. This benchmarking can be performed by using procurement analytics and purchasing Key Performance Indicators (KPIs) such as cost avoidance, purchase order cycle times, and supplier compliance rate. It aims for continuous improvement in better productivity, completion rates, and higher quality performances.
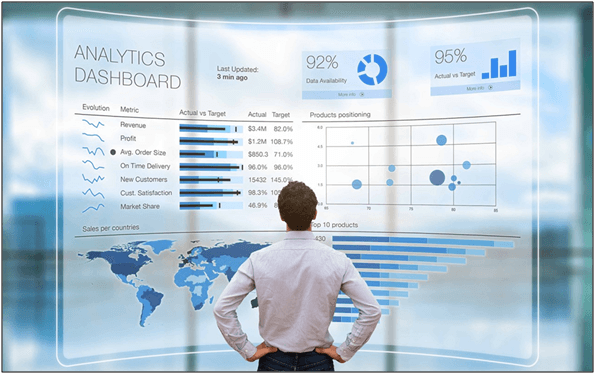
The benchmarking can be performed by reviewing own company’s past projects. The procurement team can study what are working and not-working procurement processes on the last projects. After that, they can determine how the processes can be improved. Procurement benchmarking can be performed not only internally, but also against other competitor construction companies. The competitive benchmarking information can be gathered from the published surveys conducted by third-party firms. However, competitive benchmarking is always tricky as most construction companies do not wish to release any private information. The procurement team will need to draw some assumptions on the information gathered.
The Procurement Benchmarking Process
The procurement benchmarking can help construction companies identify the impact on the own company’s procurement performance, operational effectiveness, and competitive strength. The benchmarking process needs to be taken seriously to benefit from the outcome, and the main steps are as follows:
- Identify problem areas – The initial step to perform benchmarking is recognizing which key performance indicators (KPIs) need improvement. The common KPIs to be performed by construction companies are total procurement ROI, inventory turnover rates, supply chain cycle time, supplier compliance rates, and average purchase order processing time.
- – Gathering the information is the most work concentrated in the benchmarking process. Some of the information can be gathered relatively easy such as overhead costs per project or profit margins. Some other information is difficult to be gathered such as productivity and schedule performance. Furthermore, they are also some information that does not have numbers to be analyzed, such as relationship with supplier and customer satisfaction. In this scenario, a scoring system can be used.
- – After the information is gathered, the procurement team will start to evaluate the overall procurement performance. Regardless of whether internal or competitive benchmarking is being performed, it can help to identify what are the strengths and weaknesses of the current procurement processes in the construction company. After that, the procurement team can define more effective and efficient procurement processes or solutions.
- – The procurement team will collaborate with the stakeholders and laborers to implement the improved processes or solutions. The procurement team can also try to adopt the successful procurement processes which are being used by a competitor. After the implementation, the procurement team needs to monitor the impact of the new process and continue performing the benchmarking to keep improving the procurement process.
Investing in Cloud-based Procurement Tools
Investing in cloud-based procurement tools allows a construction company total control and oversight of goods and services spending. The cloud-based procurement tools can modernize a construction company’s procurement services by efficiently handle the process of ordering, sourcing, procuring, and handling payments.
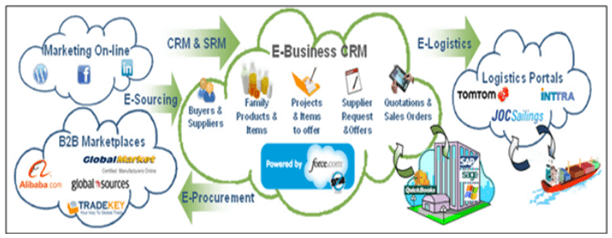
A construction company can use cloud-based procurement tools to keep the business under control, shortlisting and selecting the best suppliers, enforce the company policies and appraise supplier risk. It can also reduce the overall number of manual transactions throughout the entire procurement process which is time-consuming. Other than that, it also allows a construction company to create purchase orders, evaluate contract negotiated prices and terms, manage documents, and process non-manual supplier invoices. In addition, cloud-based procurement tools also create transparency between management and other employees, as the status of the procurement process is notified of changes instantly.While benefiting from the e-Procurement features, such as spend analysis, request-for-quotation (RFQ), reverse auction, purchase order and invoice automation, and contract management, the cloud-based procurement tools centralize all the data and documents on the cloud. This means that buyers and suppliers who are using the different types of procurement systems can communicate more efficiently using cloud connectivity and increase data visibility, sharing, and compliance. This encourages faster data collection rates that require less effort.
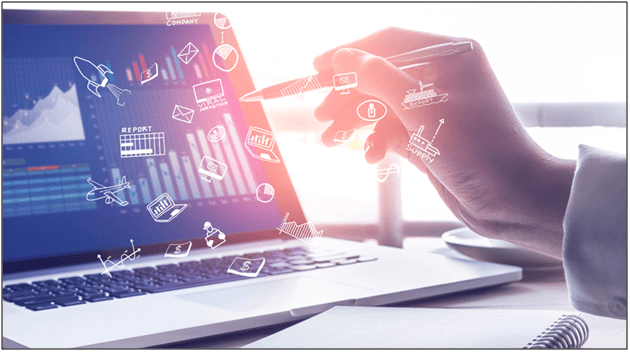
Practicing Strategic Collaboration in Procurement
With advanced technologies introduced, new geographies and supply markets have opened up. Hence, the speed and complexity of business have been increased. A procurement team needs to maintain a collaborative relationship with business stakeholders and other employees in order to create a faster and easier implementation process and more effective sourcing events. With the stakeholders involving more in the sourcing process and aware of exactly what suppliers are involved, they are more likely to approve the purchasing of products and services.
A construction company will need to work closely together with the supplier to create significant value and help supply chains become more resilient. They can work together to develop innovative new products which can boost revenues and profits for both parties. It can also help both parties to perform supply-chain optimization to reduce waste and redundant effort. Nevertheless, they can collaborate in forecasting, planning, and capacity management in order to mitigating risk and improve service levels.
The full content is only visible to SIPMM members
Already a member? Please Login to continue reading.
References
Agustin Gutierrez, Ashish Kothari, Carolina Muzuera, and Tobias Schoenherr. (2020). “Taking supplier collaboration to the next level”. Retrieved from https://www.mckinsey.com/business-functions/operations/our-insights/taking-supplier-collaboration-to-the-next-level, accessed 20/03/2021
Alex Benarroche. (2020). “What is construction benchmarking”. Retrieved from https://www.levelset.com/blog/construction-benchmarking/#What_is_construction_benchmarking, accessed 20/03/2021.
Kevin Shuler. (2020). “Top 7 Procurement Best Practices You Should Be Following”. Retrieved from https://quandarycg.com/what-are-procurement-best-practices/, accessed 20/03/2021.
Michelle Wan, PDPM. (2017). “Eight Key Strategies to Reduce Cost in the Construction Sector“. Retrieved from SIPMM: https://publication.sipmm.edu.sg/eight-key-strategies-reduce-cost-construction-sector/, accessed 18/03/2021.
Procurement News. (2018). “e-Procurement and Cloud Computing – A new Era”. Retrieved from https://blog.procureport.com/eprocurement-and-cloud-computing-a-new-era/, accessed 20/03/2021.
Sylvia Lee, GDPM. (2017). “Key Success Factors for an Effective Procurement or Purchasing Process“. Retrieved from SIPMM: https://publication.sipmm.edu.sg/key-success-factors-for-an-effective-procurement-or-purchasing-process, accessed 18/03/2021.
Thought Leadership. (2019). “What is Procurement Strategy in Construction?” Retrieved from https://www.towereight.com/what-is-procurement-strategy-construction/, accessed 20/03/2021.
Vivien Cheah Khar Wai, DPSM. (2018). “Six Procurement Best Practices for the Construction Industry”. Retrieved from SIPMM: https://publication.sipmm.edu.sg/six-procurement-best-practices-construction-industry/, accessed 18/03/2021.