Inventory control varies from one organization to another. This simplifies that the nature of firms and the nature of the businesses determine the size and category of inventory control systems and techniques to adopt. The respondents shall include all personnel who have been assigned to carry out stock control functions and all related activities. Inventory Control can also be defined as a “coordination and supervision of the supplies, distributions, storage and also recording of materials to maintain the quantities.
Table of Contents
A Well-Designed Inventory Plan
A well-defined inventory optimization strategy should include the support of the senior sales or buyer in the team because inventory optimization can affect all functions and processes within the organization. Inventory optimization shall include periodic evaluations of the organization’s supply chain itself so that inefficiencies can be well-addressed. Organizations shall develop a partnership with suppliers so that they can work to improve on inventory replenishment speed and efficiency. A kick starts with the alignment of internal and external roles, responsibilities, and accountabilities. Organizations should then map and structure their processes to determine areas for improvement and establish standardized processes that can be adopted by stakeholders.
Inventory Planning and Control Techniques
Inventory planning allows companies to get control over the business by making inventory more accessible by a product’s popularity and by scheduling production. Inventory planning is known as a process that companies follow when deciding on the quantity of a product needed and when production should start to fulfil sale orders within the business’s production capacity.
Some techniques for Inventory Control are as follows:
- First In, First Out (FIFO)
- Minimum Order Quantity
- ABC Analysis
- Last In, First Out (LIFO)
- Perpetual Counts
- Just-In-Time (JIT)
- Safety Stock
First In First Out (FIFO) Technique
First in first out simplifies the materials you received first are the items you have held longest and therefore closest to obsolescence or expiry. To avoid worthless inventory, organizations move these products before they cannot be sold.The FIFO method applies to both warehouse inventory management and accounting department where valuation method is use. High accuracy inventory valuation methods, an organization’s financial statements reflect reality as accurately as possible. Mandatory for staff personnel making smart decisions.
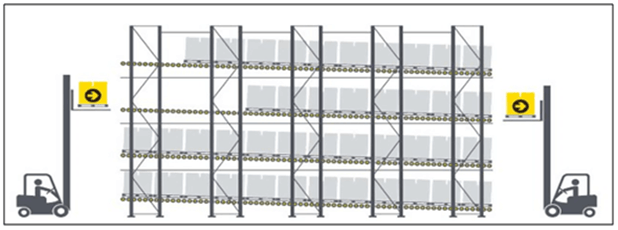
Minimum Order Quantity Requirements
Many suppliers and vendors must set minimum order standards for each item or material that they carry. It helps to keep the costs down when ordering products wholesale but means that business owners must order a certain amount each time.
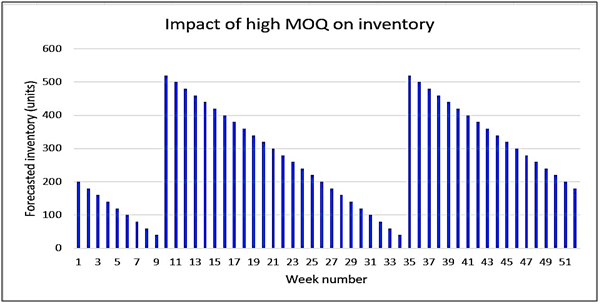
Typically, items categorized under an inexpensive cost will have higher minimum order quantities. Repeatedly this allows wholesale merchants to sell items at a lower cost. To an extent, it is the retailer’s advantage, but it is important to be aware not to over order and leave the store with a stock surplus. The smaller the order quantity submits, the more these costs affect the profit margin.
ABC Analysis Inventory
ABC inventory analysis is defined as the process for examining inventory to determine exactly how much the organization needs to hold. Inclusive of the insight this analytical approach provides businesses to identify huge opportunities to reduce inventory levels. Focusing their time and energy that represent huge sales.
A good start for inventory to be divided into three core categories based on their strategic importance.
- A-items: Products that are important and thus require tight controlling
- B-items: Products of lower importance but still be managed with a medium level of control
- C-items: Products of lower importance that require the simplest and often the easiest level of control
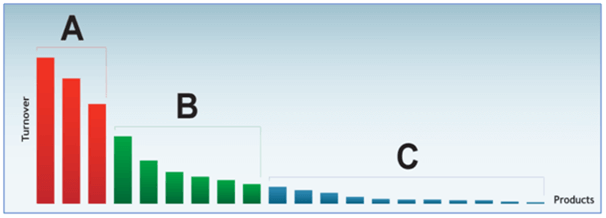
Last in First Out (LIFO) Technique
LIFO method complies well with the matching principle in a way as it charges the costs with revenues from a similar period. Revenue and costs are expressed in the most recent value. In certain industries, LIFO is most suited as it conforms with the actual physical flow of the inventory. If prices rose during the period but when at year-end prices have fallen, then most probably ending inventory do not need to be written down as the newest units with high costs are already consumed and ending inventory is based on the actual cost that was prevailing before the hike.
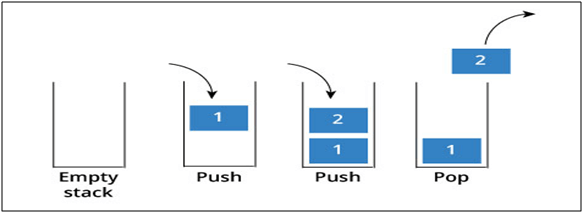
Perpetual Counts Technique
A perpetual inventory system allows the management to track information against physical inventory for any discrepancies. Particularly to check for theft, human errors, and spoilage of items. Systematically, saving time as staff personnel no longer have to conduct a tedious inventory count every day to determine what is the amount of stock available in the warehouse. By continually recording all the data analysis for sales, returns, discounts and other miscellaneous transaction reports. All relevant stakeholders can have access to important data at any time access. This allows businesses to keep up with the real-time demand of items and make necessary adjustments as information becomes available in-depth.
The full content is only visible to SIPMM members
Already a member? Please Login to continue reading.
References
Lee Yi Xian, DLSM. (2020). “Inventory Control Techniques for Effective Warehousing”. Retrieved from SIPMM: https://publication.sipmm.edu.sg/inventory-control-techniques-effective-warehousing/, accessed on 13/09/2020.
Lim Hun Meng, GDCSM. (2019). “Data Analytics for Optimizing Inventory”. Retrieved from SIPMM: https://publication.sipmm.edu.sg/data-analytics-optimising-inventory/, accessed on 14/09/2020.
Melanie. (2019). “How Setting Par Levels Can Help Improve Your Inventory Control”. Retrieved from “https://www.unleashedsoftware.com/blog/setting-par-levels-help-improve-inventory-control”, accessed on 13/09/2020.
Supplychainbrain. (2020). “A Well-Designed Inventory Planning & Optimization Strategy Must Be Maintained”. Retrieved from “https://www.supplychainbrain.com/articles/12714-a-well-designed-inventory-planning-optimization-strategy-must-be-maintained”, accessed on 12/09/2020.
Tradegecko. (2020). “What is a Perpetual Inventory System?”. Retrieved from “https://www.tradegecko.com/inventory-management/what-is-perpetual-inventory-system”, accessed on 14/09/2020.