Reverse Logistics is a money-burning business. A weak reverse logistics process brings the worst to the company. In recent years, many businesses have started to venture into this field when they realized its potential of helping them achieve business sustainability. Indeed, a good reverse logistics design can have cost-saving, sales-increasing, and gain a competitive advantage.
The design of the optimized reverse supply chain model is crucial in helping enterprises save cost and gain benefits from their supply chain. Therefore, the benefits that a business will reap from practicing a good reverse logistics system will outweigh what they have paid for in the long run.
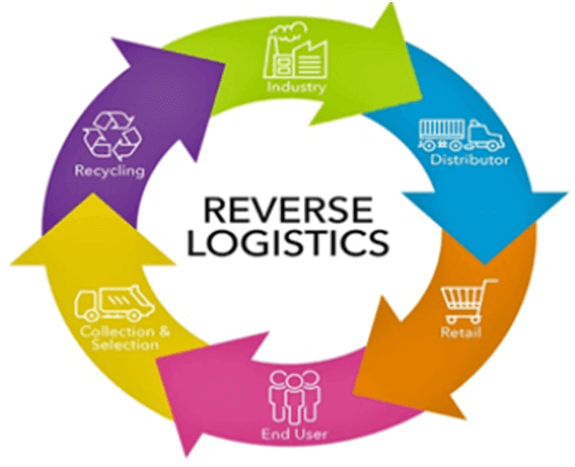
Table of Contents
The Harm from Toxic Wastes and the Causes
It is not surprising for many to underestimate the detrimental impacts that toxic wastes are currently bringing to our environment which directly affects our daily lives. Many types of toxic wastes have been generated during the process of technology development and advancement, as shown in the pictures below.
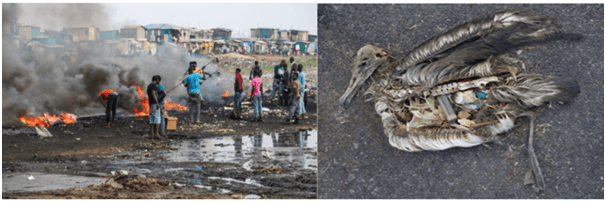
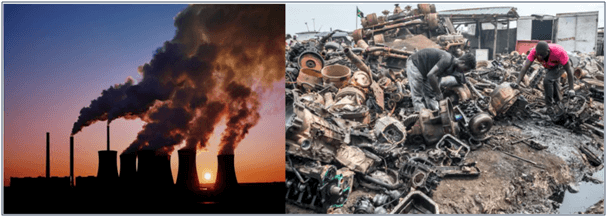
The key causes for rapid growth in the amount of wastes are:
- Over-population
The continually increasing human population is causing a rise in all types of pollution (air, water & land)
- Urbanization.
A shift from rural lifestyle towards urbanization will lead to an increase in wastage
- Affluence
With production or per capita consumption, there is a trend to declare items as obsolete, resulting in their abandonment.
- Technology
A growing trend in technology advancement for most economic goods is leading to returnable packaging to nonreturnable packaging.
Lean Procedures for Reverse Logistics
Lean procedures play an important role in the Reverse Logistics process as that determines whether the Reverse Logistics will bring benefits to them or the opposite. Facilities that do not develop Lean procedures for returning, processing, re-manufacturing, part disposal, repairing, and replacing products may create a lot of unnecessary wastes. Resourcefully managing the reverse logistics process, nevertheless, increases profitability and adds value for customers.
To reduce wastes in the reverse logistics procedures, focus on movement and processing, which can be significant sources of inefficiency and waste. Think about facility layout, item flow, and worker skill and movement. Workers must be capable to sort and break down returns with minimal movement, ensure all information, tools, packaging material, and other materials are nearby with a specific assigned place. Process, data collection, and activity charts can be useful in this analysis.
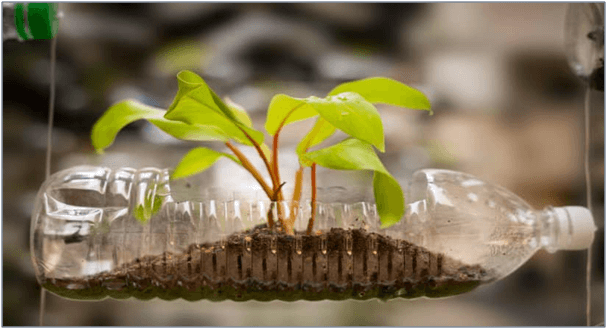
Establishing a Lean Return Process
The returns process included the company’s return policy (which can be generous or strict), operations outsourced to third-party logistics (3PL) providers, Return Material Authorization (RMA) procedure, Warehouse Management System (WMS), and technology tools. All these factors have a great impact on whether the returns process is well-organized and Lean.
When developing a reverse logistics process, consider the following factors:
- Prevention. Use Lean tools such as Quality at the Source to lessen returns.
- Financial incentives. Prevent processes such as demanding returns back to the sales department that cause RMA delays.
- Core competencies. If the company lacks reverse logistics expertise, consider subcontracting this function to a 3PL that can manage it efficiently.
- Suppliers. For a wholesaler or retailer, review the returns handling terms with vendors.
- Cycle times. Assess the entire returns process from starting with the customer, RMA procedures, and reverse logistics network in order to identify probable sources of waste.
- Technology. Spend on the right tools to help to control and measure the reverse logistics process.
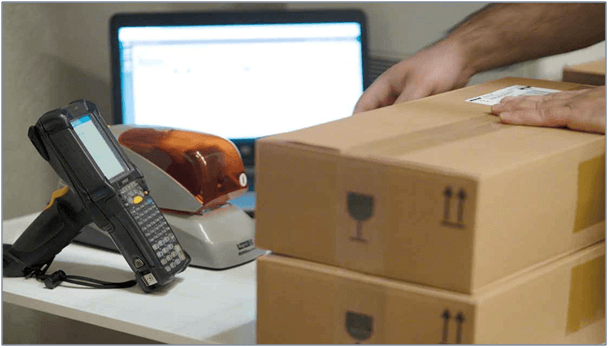
Using Lean Practices to Convert Reverse Logistics to Cash
All of us know about the various challenges that reverse logistics will be bringing to businesses – costly, complexity on the returns process, inadequate labor resources to handle the return, poor visibility into the products received, and other problems. But Lean procedures can help.
Supposed a company has no monitoring systems for the returning processes in place, and is accepting all the goods that customers are requesting to return. In this way, the company is going to suffer losses as there is a chance that customers will return goods that are not acceptable. On the other hand, with a unique reference attached for each good, the company can implement a portal that allows customers to check on the status of their goods to confirm that they are returnable before proceeding to do so. With this additional layer added, the company minimizes the risk of them receiving non-returnable goods.
With Lean put into practice, a constructive return policy is critical in helping a company reduce costs and increase profits. In order to do so, companies might need to consider prohibiting the return of the following products:
- Consumable product (e.g. Battery parts)
- Lower cost product (e.g. Part value less lower than $50)
- Zero business values product (e.g. A legacy product that no longer has demand in the market.)
- High scrap rates product (e.g. A product that not easy to sustain and difficult to repair)
Lean Methodology
There are many various kinds of LEAN tools that are widely used among companies all over the world which most of you might be familiar with. Lean is a compilation of best practices and tools whose focus is to eliminate waste, add customer value, increase speed, and ensure capability.
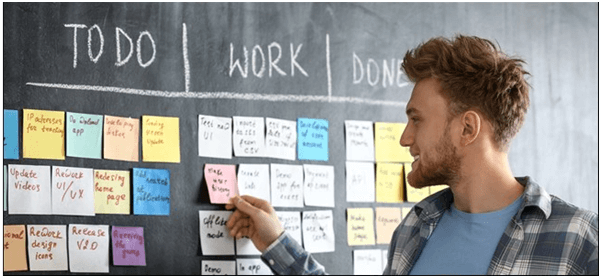
- The Kaizen techniques
It is an endless improvement strategy that focuses on better ideas involving every aspect of a corporation.
- Six Sigma
It is a set of Lean management tools and techniques designed to develop business by reducing the probability of error. It is a data-driven approach that uses a statistical methodology for eliminating defects.
- Muda
The “Eight” Wastes that consist in the process: Transportation, Inventory, Motion, Waiting, Over-Production, Over-Processing, Defects, Skills Unutilized
- Poka-yoke
The best way to reduce errors and defects is not to have them in the first place. Prevent first, remove opportunities for errors to occur. Allow people to use their intellect to improve the process, not try to determine how not to make mistakes.
- The 5S Methodology
5S is the foundation of the organized workplace. It brings visibility to the condition of the work and the workplace. The 5S stands for Sort (Seiri), Set in Order(Seiton), Shine(Seiso), Standardize(Seiketsu), Sustain (Shitsuke).
- Kanban
Kanban (看板) is a visual scheduling system for managing work as it flows through a process.
Conclusion
There are many kinds of Lean tools that can be facilitated within Reverse Logistics processes. Using the Lean Methodology helps by overseeing all elements of supply chain providers and participants. Moreover, it can also help to maintain the value of goods throughout the whole process with additional work required for performing data collection or tracking relevant information. In addition, it is undeniable that a well-organized reverse logistics operation can be a win-win proposition since it correlates well with today’s increased focus on business sustainability with the aim of reducing costs, improving the company’s reputation, and achieving greater customer satisfaction. Ultimately, it can be used to establish a competitive advantage for the business.
References
Clover Lee, PDLM. (2019). “The Reverse Logistics for Plastic Materials”. Retrieved from SIPMM: https://publication.sipmm.edu.sg/reverse-logistics-plastic-materials, accessed 8/12/2020.
Gimbal Team, (2009), “Lean 101 – Part 3: The Eight Wastes”. Retrieved from GIMBAL: https://gimbalcanada.com/lean-101-eight-wastes/ accessed 09/08/2020.
Neil Sharp, (2013). “What is takt time, why is it important and how to calculate it”. Retrieved from JJS Manufacturing https://www.jjsmanufacturing.com/blog/what-is-takt-time-why-is-it-important-and-how-to-calculate-it, accessed 8/10/2020.
Paul A. Myerson (2013). “Putting a Lean Spin on Reverse Logistics”. Retrieved from Inbound Logistics.com: https://www.inboundlogistics.com/cms/article/putting-a-lean-spin-on-reverse-logistics/, accessed 8/12/2020.
Theresa Pang Kim Lian, DLSM. (2019). “Key Considerations for Reverse Logistics Operations”. Retrieved from SIPMM: https://publication.sipmm.edu.sg/key-considerations-reverse-logistics-operations, accessed 8/12/2020.
Yvonne Ong Hwee Ping, DPSM. (2020). “Lean Procurement Practices for Reducing Food Waste”. Retrieved from SIPMM: https://publication.sipmm.edu.sg/lean-procurement-practices-reducing-food-waste, accessed 8/12/2020.